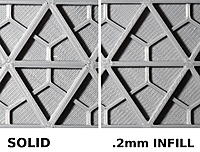
For the standard lion settings of .2mm layer height & .4mm line width, z coordinates have to be a multiple of .2mm. Wall thicknesses have to be a multiple of .4. Cura doesn’t enforce the multiples for some reason. It does enforce a minimum top & bottom thickness of .4mm.
A fiendish problem lions chased for weeks was ridges in horizontal surfaces. Horizontal pieces have to be at least 1.2mm thick to get a smooth top surface. That creates .4mm of top thickness, .4mm of bottom thickness, & .4mm of infill.
If the piece is 1mm thick, it needs to have .2mm of infill & will have a ridged but bearable top surface. If the piece is .8mm thick or is solid, it’ll have no infill & unbearable ridges in the top surface. The printer needs a void between the top & bottom to push in excess filament. Ironing literally pushes filament into the infill.
For pieces over 1.2mm thick, the issue becomes how thick the top & bottom shell can be, since the only force is the top layer against itself instead of against the bottom layer. There is a certain limit beyond which it’ll form ridges, probably .8mm.
Parts have to be printed so forces transfer along the filament lines rather than between layers. This results in funky orientations, but resolution in the Z direction is also a lot less than resolution in X & Y. Parts have to be designed with the printing orientation & .2mm resolution in whatever direction has to be Z.
There is always using a .1mm layer height, but this has not given enough improvement to be worth it. Cura doesn’t allow top & bottom thickness below .4mm so .1mm layer height doesn’t buy thinner parts. Lions sometimes use a line width of .28mm just to make something waterproof, not to increase precision. This too has been too little improvement to justify it. Changing to a .2mm nozzle just to print a small part hasn’t been worth the effort, but maybe someday.
Elephant’s foot + horizontal expansion adds .5mm to the total width of a part or .25mm to each side. Horizontal expansion alone adds .3mm to the total width or .15mm to each side. This changes if the line width isn’t .4mm or the layer height isn’t .2mm. It also depends on the size of a layer, whether the side is convex or concave.
Parts have to be modeled as single polygons to get printed with a single continuous piece of filament. If subdivisions & triangles are modeled as separate polygons, it won’t join the 2 shapes with a single filament.
Isogrids really do have structural value in the small scale plastic world. When sliced right, they’re roughly as strong as solid plastic, but use much less material.
This article was first featured at https://www.rcgroups.com/forums/showthread.php?3732085-Printing-small-parts&goto=newpost on October 14, 2020 at 03:53AM by Jack Crossfire
More Stories
Can this possibly be true? “Metal 3D printing is now possible on any 3D printer…with the right settings and a few minor upgrades like a hardened steel nozzle…” – July 2 2023 at 04:59PM
New NASA Funding Ignites 25 3D Printing Projects in Space Exploration – June 18 2023 at 04:34PM
Nvidia AI produces 3D models from 2D videos 3D printing applications forthcoming? – June 15 2023 at 02:55AM