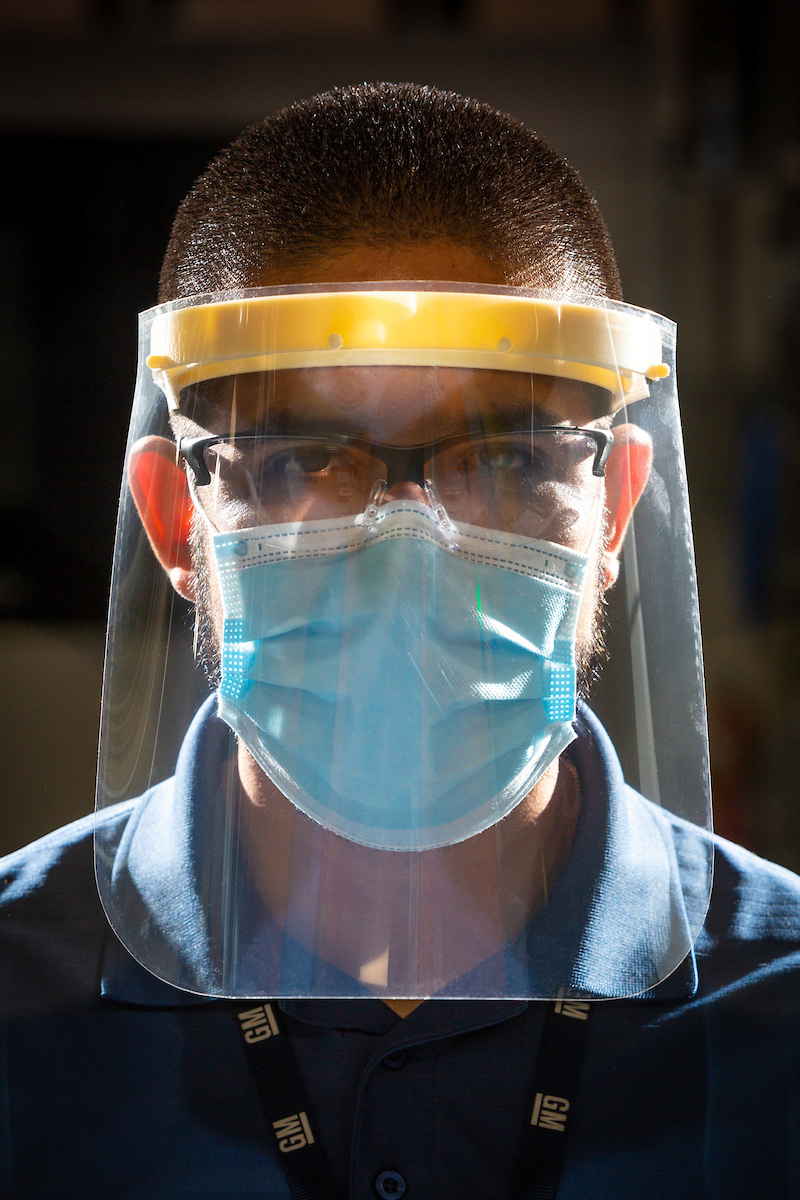
-
General Motors 3D-printed parts for more than 17,000 face shields that were donated to hospitals and first responders. [credit:
Jeffrey Sauger for General Motors
]
The COVID-19 pandemic has changed the way many of us work, and that is certainly true for General Motors. The nation’s largest automaker might not be selling nearly as many cars as it hoped and has even pushed back some of its product releases (like a refreshed Bolt EV), but it’s been plenty busy. The company has switched gears and is using its resources and expertise to build ventilators and personal protective equipment like face shields to supply the healthcare sector. As it turns out, General Motors’ investment in additive manufacturing—3D printing to you and me—has played a big role in getting that effort up and running quickly.
Covid-19 Coverage
- GM makes cars; how did it quickly pivot to face shields and ventilators?
- WHO gives up on hydroxychloroquine for COVID-19, stops trials
- As COVID-19 cases increase, Pence blames prevalence of testing
- Mutation may be helping the coronavirus spread more readily
- COVID-19 death rate cut by cheap steroid, according to unpublished data
GM is no stranger to 3D printing, having first dipped a toe into the world of additive manufacturing back in the late 1980s. These days, as the technology has matured, GM mostly uses it for rapid prototyping and testing new parts. But it has also been invaluable in making medical supplies.
“The ventilators maybe got a lot of the headlines here,” explained Kevin Quinn, GM’s director of additive design and manufacturing. But there was also Project O, “as in ‘other,’ like everything else, right? What else could we do to help support the frontline and support the healthcare workers as they were really battling this tooth and nail every day? And that was where the face shields, the ear savers, some of these other projects were born,” he told me.
Read 12 remaining paragraphs | Comments
This article was first featured at https://arstechnica.com/?p=1684699 on June 18, 2020 at 08:33AM by Jonathan M. Gitlin
More Stories
Can this possibly be true? “Metal 3D printing is now possible on any 3D printer…with the right settings and a few minor upgrades like a hardened steel nozzle…” – July 2 2023 at 04:59PM
New NASA Funding Ignites 25 3D Printing Projects in Space Exploration – June 18 2023 at 04:34PM
Nvidia AI produces 3D models from 2D videos 3D printing applications forthcoming? – June 15 2023 at 02:55AM